This article has been reviewed according to Science X's editorial process and policies. Editors have highlighted the following attributes while ensuring the content's credibility:
fact-checked
trusted source
proofread
Designing cameras for harsh environments? Be sure to account for lens mount details
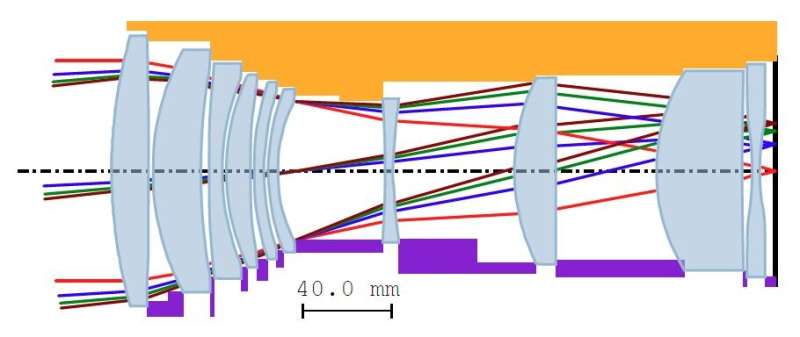
Cameras used in harsh environments must be designed in a way that prevents temperature swings from influencing their optical performance. New research demonstrates that accounting for the exact lens mounting structure used is a critical step in ensuring that lens systems remain robust to temperature changes.
Eric M. Schiesser from Synopsys, Inc. will present the new research at the Optica Design and Fabrication Conference, which will take place June 4–8 2023 in Quebec City, Canada.
"Most optical systems—from the camera in your smartphone to the eyes of the Mars rover—are used over a range of temperatures. To keep the image sharp over the changing temperature, optical engineers can fine-tune the details of the optical and mechanical designs so that the thermal effects balance each other. Everyone involved in the manufacture of these passively athermalized optical systems should appreciate how interwoven the mounting structure is to the optical prescription, which is the thrust of our design study," said the research team.
Both the glass used to make lenses and the materials used to make the mounts that hold lenses are sensitive to changes in temperature, which can make optical systems lose focus when temperatures rise or fall. However, it is possible to reduce variations in optical performance over a range of temperatures using a process called athermalization, which achieves optothermal stability by incorporating several materials with different thermal properties.
In the new work, the researchers focused on using passive athermalization to mitigate thermal effects. This involved designing the lens system and mounting structure so that the thermal shift of the optimal focal plane matched the mechanical shift of the focal plane array used as the detector in the camera.
To illustrate the importance of accounting for lens mounting details, they performed athermalization for the same camera lens using two different lens mount structures. They first analyzed the thermal behavior for a seat model in which the lenses are held against seats integrated into the mounting structure or housing. In this case, the mounting structure itself provides the connection between the seats, which means that the thermal expansion of one element doesn't affect the position of any other element.
The researchers athermalized the seat model lens across a given temperature range by changing the surface shapes, element thicknesses, lens separations and lens materials. Then, they re-analyzed it using a spacer-based mounting approach. In a spacer-based housing concept the lens system is a stack of lenses and spacers. For a given temperature increase, glass will expand less than most materials used as spacers, which means that the expansion of the spacers will create a greater effect than the expansion of the lenses themselves.
A performance comparison for the different lens mount configurations showed that when the mounting method was changed, the focal plane array became out of sync with the optimal image plane because the lens elements don't respond to temperature changes in the same way. The researchers note that this performance degradation in is not inherent to a spacer-based mounting structure. If the original athermalization was carried out assuming spacers, switching to seats would also degrade the performance.
Overall, the study shows the importance of accounting for the specific mounting structure used when performing passive athermalization and that changing the mounting characteristics after athermalization will likely lead to poor thermal stability.
Provided by Optica